EXTENDED ABSTRACT
Pawel Pocwiardowski 1
The last couple of years exacerbated the shortage of resources to conduct hydrographic surveys for dredging industry. At the same time the companies started to invest in USVs (Unmanned Surface Vehicles) or small SV (surface vehicles) to improve the mobilization time and reduce the overall “footprint” of the operation. In this paper, we present a paradigm change in managing the essential hydrographic surveyor resources by utilizing the technology to divide the dredging hydrographic survey into two parts, design and execution of the survey. The survey “design” is done by a hydrographer or survey manager operating from the remote location setting up the essential parts of the survey. Then the survey execution is done by a skipper or USV operator at the actual job site. These two are connected via a dedicated software which seamlessly combines these two functions into one consolidated efficient solution.
The essential feature of the presented solution is that it allows a concurrent operation of the remotely located hydrographer and the local operator conducting the survey. The architecture of the system has been designed to facilitate the remote access and perform advanced tasks by the hydrographer while the operator uses the hand-held device to conduct the survey.
The hydrographer accesses the system on the USV remotely via web browser and sets up the mission. He prepares the design template satisfying the required clearance, ensures that the proper reference system, geodesy and other required items are chosen correctly. He prepares the local station offset file, the survey lines over for the vessel to run and loads it in the system, so the operator can easily see where to drive the boat. With that he prepared the background image overlayed on the map which loads to all connected displays. While the hydrographer sets up the system, the operator uses hand-held device and can observe the effect of that work.
When the survey is prepared, the operator starts the survey and collects the data. Concurrently, the hydrographer can independently access the data with his own displays, checks the coverage, plots and checks the profiles without disturbing the operator (Fig. 1). Hydrographer can verify the quality of the data by examining the standard deviation of the collected data and even seamlessly transfer the data to GIS software via build in WMS and WFS interface for further tasks such as report generation, volume computation and other processing tasks. When the survey is over the collected raw data can be reprocessed for the final delivery.
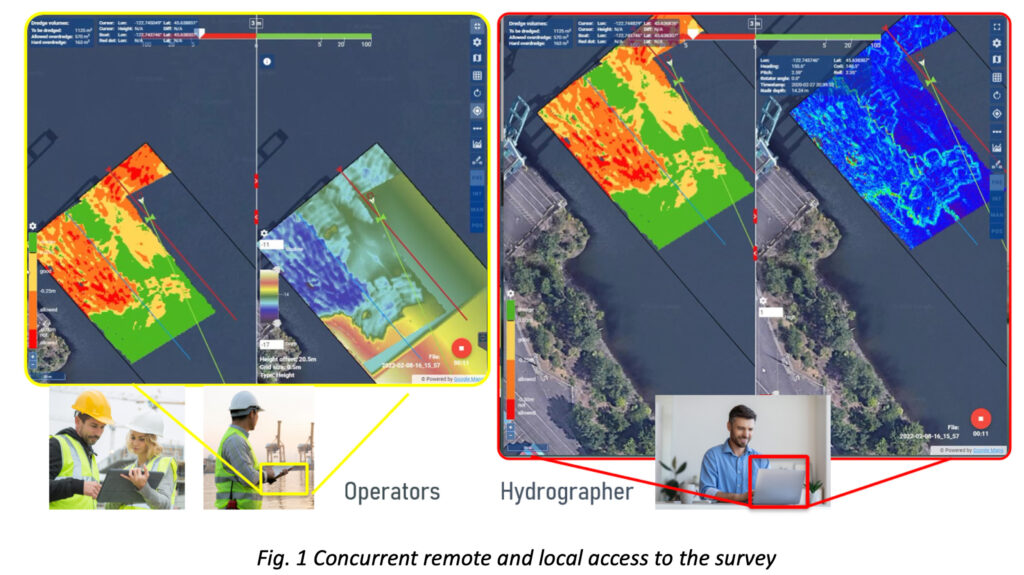
In this paper we introduce new paradigm in hydrographic surveying for dredging industry. This new approach allows fully utilize the surveyor’s experience to prepare and manage the survey allowing to use the needed skills more efficiently to run concurrent remote surveys. At the same time, the solution allows the skipper or the operator to manage the execution part of the survey with simple hand-held device. Dredging companies can lower operation costs by using hydrographers for the critical part of the survey and then utilizing skippers and operators to drive the vessels. At the same time, this technology allows the surveyors to manage more jobs from a remote location as well as optimize the cost of their service.